Warehouse automation: from dream to reality
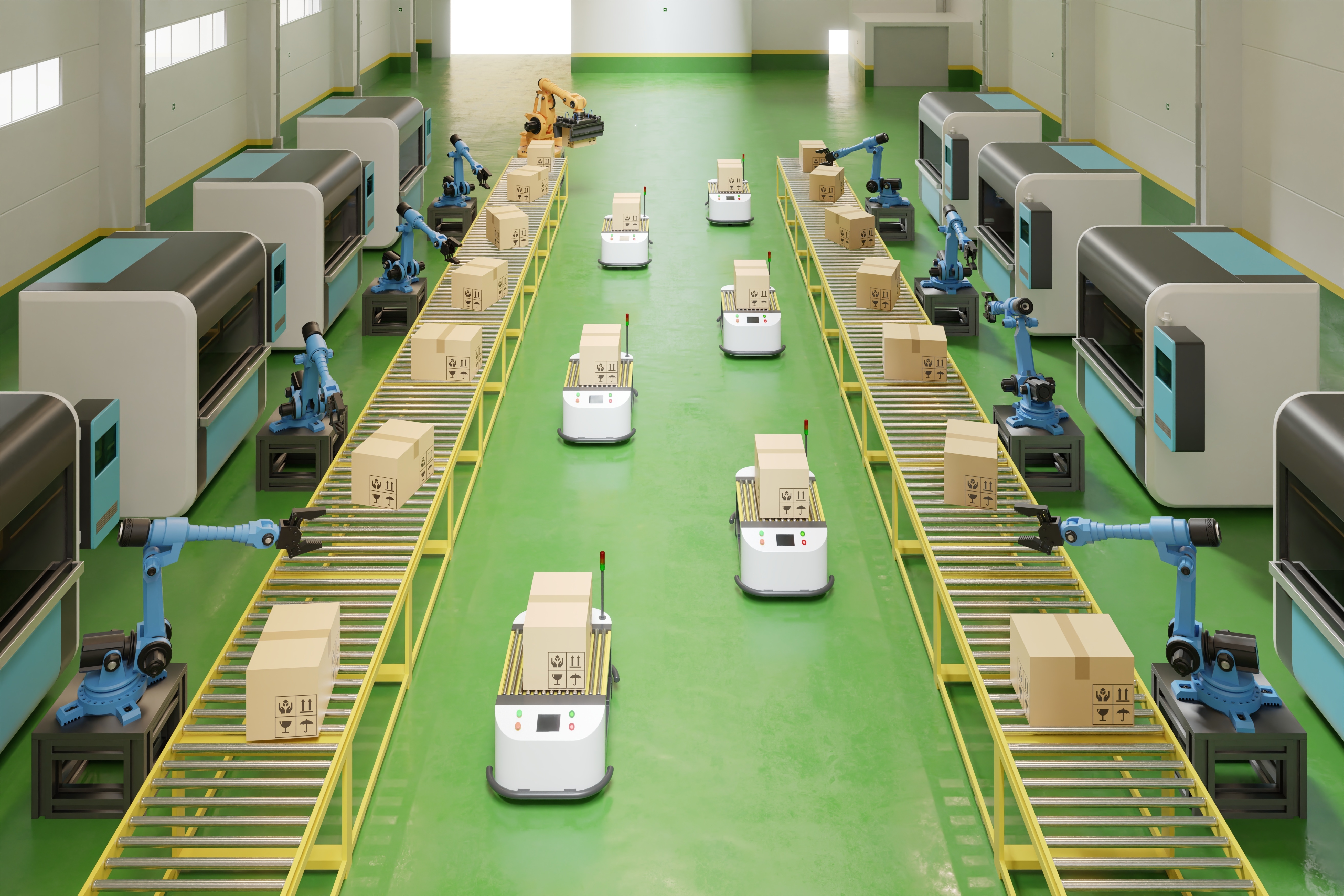
Warehouse automation offers an answer to several problems, such as variations in volumes to be processed and order preparation time. The e-commerce and food sectors are the most advanced in this area.
This is not a French or European trend, but a global one aimed at improving productivity, managing peaks in activity and above all reducing logistics costs.
In China, Alibaba has equipped its Huiyang warehouse with 60 AGVs (Automated Guided Vehicles), based on the "Goods to man" principle. These autonomous robots move around on the floor, which is covered with QR codes that enable them to identify their position in order to transport the shelves containing the articles to the order pickers. Each robot can carry up to 500 kg and has a range of 4 to 5 hours for a 5-minute charge. Alibaba has reduced human labour in this warehouse by 70%. This technology is also widely deployed by Amazon, in particular in the new site at Brétigny-sur-Orge, which uses 4,000 robots and employs 670 people recruited on permanent contracts at the opening.
Alibaba's competitor, JD.com, is not to be outdone. The JD.com warehouse in Shanghai is fully automated, from receiving items to shipping orders. An articulated arm depalletises, scans the boxes and places them in standard bins. These bins are transported on conveyors and stored by AGVs in stacker cranes. Picking is also automated, as is the packaging and labelling of the packages. Robots place individual packages on AGVs, which place them in bags on a lower level. The bags are transported by other autonomous robots to the shipping dock, before being loaded onto trucks.
A race to robotize
E-commerce, because of the low margins and the large peaks of activity to be absorbed, is certainly the sector most prone to technological innovations in order picking.
Ocado, the UK's leading online supermarket, is renowned for its automated picking solutions. Before a dramatic fire, the group's Andover-based warehouse was home to 1,100 robots that processed 65,000 orders each week. This ballet of robots navigated precise beam paths (only 5mm of space separated each robot), the surface area of which was the equivalent of several football pitches. They were directed by an air control system with 4G flow. The robots moved at a maximum speed of 4 metres per second, were battery-powered and charged autonomously at terminals. A pick and pack operation could be completed in 5 minutes, despite the 250,000 storage bays in the warehouse. The reconstruction of Andover will take two years. Ocado is now exporting its know-how to major retailers in Europe, such as Monoprix in Fleury-Mérogis, and in Japan, to the Aeon retail group.
Amazon is at the forefront of this race to robotisation. It operates 50 "robotic fulfilment centres" around the world. The one in North Haven, Connecticut, covers 79,400 m². It houses 16 km of conveyors and several hundred autonomous mobile robots. The labelling of packages is automatic after packaging. Powerful algorithms determine how to allocate millions of SKUs and more than 100 million items to the 185 supply centres to deliver on time to the end customer.[1]
But automation is not just for logistics centres. Amazon is planning a new type of supermarket in California. 21% of its surface area will be dedicated to an automated mini warehouse for e-commerce order picking.The "Goods to man" principle will be maintained, but this time with the help of a stacker crane or a shuttle and not AGVs for dry goods. Cold products will be picked up by order pickers from the shelves.
But robotisation is not limited to the distribution and e-commerce sectors.
For example, Armor, a leading manufacturer of thermal transfer ribbons in Nantes, France, has equipped its warehouses with customised AGVs designed by the Rennes-based company BA Systèmes. The picking of their semi-finished products is carried out by AGVs which place them on conveyors. The products are then palletised by a robot and packed by an automatic wrapping machine before being taken to the shipping dock. AGVs also serve the semi-finished products in the cutting plant. This development is all the more remarkable because the products are bulky, heavy (about 300 kg) and cylindrical.
Complementary software solutions
Faced with the inevitable growth of automation, software designers must offer adapted solutions. The German company Inconso, for example, has developed modelling and visualisation functions for automated systems. The partnership with the company Doks.innovation, makes it possible to offer a solution for inventories by drone. The inventAIRy® X drone detects and records all visible barcodes. This data can be transmitted directly to an ERP or a WMS.
Inconso also supported Mango in the automation of its 180,000m² warehouse in Lliça d'Amunt, north of Barcelona. Their inconsoWMS solution controls the automated transit of goods (shuttles, 25-metre high stacker crane) and ensures the connection between all areas of the warehouse. Their complementary solution inconsoDOM ensures the link between the ERP and inconsoWMS. The order preparations are planned according to the variables of the Mango ERP, and the preparation of a Mango package for shipment takes less than 120 minutes.[2]
Automation thus requires the search for new digital solutions. TGW Logistics Group, an Austrian integrator of automated solutions, has just developed a digital equivalent to its Rovolution unit picking solution, which will make it possible to analyse flows in real time and anticipate any future overruns.
In conclusion, we note that mechanical and innovative solutions are already mature and well established in many sectors, throughout Europe. The use and management of data remains a key factor of success to stand out from the competition. Automation is no longer a logistician's dream, but a reality in many sectors